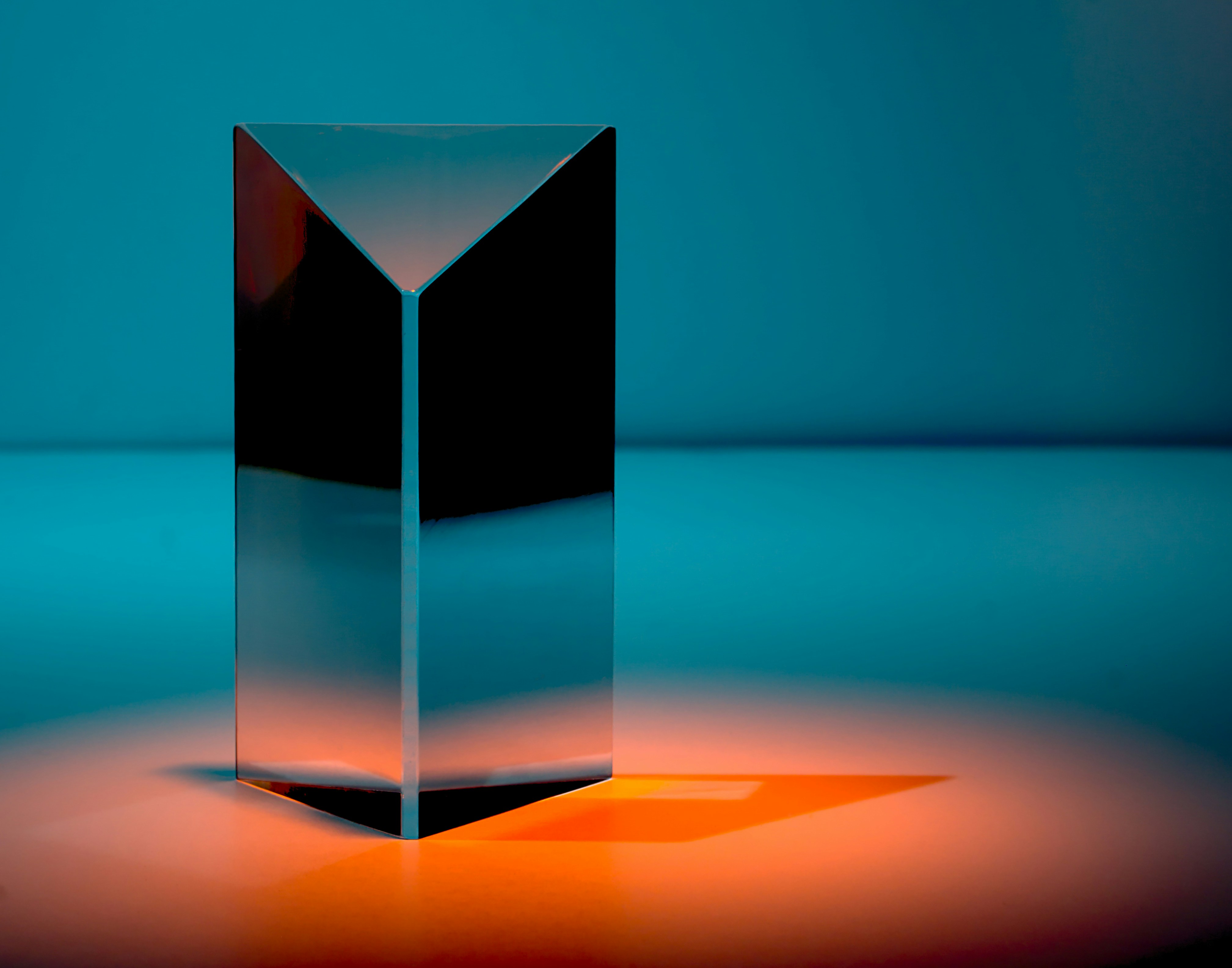
The Ultimate Glossary of Materials Science Terms: Your Comprehensive Guide to Innovative Materials
From advanced composites enabling lighter aircraft to novel alloys powering the next generation of batteries, materials science drives the breakthroughs behind countless innovations. By combining insights from physics, chemistry, and engineering, materials scientists develop, test, and refine substances critical to industries ranging from aerospace and automotive to healthcare, electronics, and energy. This glossary provides a comprehensive guide to essential terminology in materials science, helping you navigate the field’s core concepts, processes, and specialities. Whether you’re starting out, broadening your expertise, or eyeing new career opportunities, visit www.materialssciencejobs.co.uk and follow Materials Science Jobs UK on LinkedIn for the latest roles, insights, and networking events in this ever-evolving domain.
1. Introduction to Materials Science
1.1 Materials Science
Definition: An interdisciplinary field studying the properties, structure, and performance of substances—be they metals, polymers, ceramics, or composites—to tailor them for specific applications.
Context: Materials scientists bridge physics, chemistry, and engineering to discover or improve materials. Their work underpins product design in aerospace, biomedical devices, consumer electronics, and more.
1.2 Materials Engineering
Definition: Translating knowledge from materials science into practical solutions—developing processing methods, shaping final properties, and scaling manufacturing processes.
Context: Materials engineering often merges lab discoveries with industrial needs, ensuring a new alloy, polymer, or ceramic can be produced consistently at scale.
1.3 Classification of Materials
Definition: Materials generally fall into categories—metals, ceramics, polymers, composites, and semiconductors—each with characteristic bonding, structure, and mechanical or thermal properties.
Context: Classification helps in selecting the right material for a design. E.g., metals for conductivity and strength, ceramics for high-temperature resistance, composites for lightweight strength, etc.
2. Fundamental Concepts & Classifications
2.1 Crystalline vs. Amorphous
Definition:
Crystalline: Atoms arranged in a regular, repeating lattice (e.g., metals, many ceramics).
Amorphous: Random atomic arrangement (e.g., glass, certain polymers).
Context: Crystallinity influences properties like strength, melting points, or optical clarity. Amorphous solids (glasses) may be less brittle at certain temperatures or more transparent.
2.2 Phase Diagram
Definition: A chart mapping stable phases (solid, liquid, gas—or multiple solid phases) of a material system under different temperatures, pressures, or compositions.
Context: Phase diagrams guide alloy design, indicating transformations (eutectic, peritectic), melting points, or solid solutions. They’re key to controlling microstructures in metals or ceramics.
2.3 Microstructure
Definition: The arrangement of grains, phases, or defects within a material visible under a microscope (optical, electron). Microstructure strongly affects mechanical properties.
Context: Microstructural analysis helps predict failure modes (cracks, corrosion), tailoring heat treatments or doping to refine grain sizes for desired performance.
2.4 Stress-Strain
Definition: Stress measures internal forces per unit area, while strain quantifies deformation relative to original dimensions—fundamental in mechanical testing (tensile, compression).
Context: Stress-strain curves reveal yield strength, ultimate tensile strength, and elastic moduli. They define how materials will behave under loads.
3. Structure & Properties of Materials
3.1 Crystal Lattice & Unit Cell
Definition: The repeating 3D array of atoms in a crystalline solid. The unit cell is the smallest repeatable structure capturing its lattice symmetry.
Context: Lattice geometry (FCC, BCC, HCP) influences slip systems, ductility, or conductivity. E.g., FCC metals (aluminium, copper) are often more ductile than HCP (titanium) metals.
3.2 Polymorphism / Allotropy
Definition: The ability of a solid to adopt different crystal structures depending on temperature or pressure (e.g., iron changes from BCC to FCC at certain transitions).
Context: Polymorphism affects mechanical behaviour (like steels). Carbon allotropes (graphite, diamond, graphene) exemplify how structure drastically alters properties.
3.3 Defects (Dislocations, Vacancies)
Definition: Imperfections within crystals (missing atoms, dislocations, grain boundaries) that can heavily influence strength, ductility, or conductivity.
Context: Dislocations enable plastic deformation. Controlled introduction or removal of defects can strengthen metals (cold working) or degrade them (creep, fatigue).
3.4 Thermal & Electrical Conductivity
Definition: A material’s capacity to transmit heat or electrical current, influenced by bonding, electron mobility, and structure.
Context: Metals typically excel in electrical conduction (free electrons), ceramics insulate due to electron localisation. Polymers vary widely depending on doping or composition.
4. Processing & Manufacturing Techniques
4.1 Casting
Definition: Pouring molten metal into a mould, solidifying to form shaped parts. Common in automotive, machinery components.
Context: Casting can produce complex geometries but watch for shrinkage, porosity, or grain structure variations.
4.2 Sintering
Definition: Fusing powder particles (ceramics, metals) at high temperatures below the melting point—allowing diffusion-based bonding.
Context: Sintering is crucial for making ceramics, powder metallurgy products, or advanced composites, controlling final density and grain growth.
4.3 Extrusion / Injection Moulding
Definition: Methods shaping thermoplastic or metal (powder + binder) by forcing molten material through a die (extrusion) or injecting it into mould cavities (injection moulding).
Context: In polymer manufacturing, injection moulding suits mass production. Metal injection moulding (MIM) merges powder metallurgy with injection processes.
4.4 Heat Treatment
Definition: Controlling heating/cooling cycles to alter a material’s microstructure—e.g. hardening, annealing, normalising—to meet required mechanical properties.
Context: Quenching and tempering can yield tough steels. Annealing relieves internal stresses or improves ductility.
5. Characterisation & Testing Methods
5.1 XRD (X-ray Diffraction)
Definition: Using X-ray patterns diffracted by crystal planes to identify phases, lattice parameters, or stress states in crystalline materials.
Context: XRD reveals phase composition (e.g. alpha, beta phases in titanium), gleaning microstructural changes post-heat treatment.
5.2 SEM / TEM (Electron Microscopy)
Definition:
SEM: Scans a surface with an electron beam, generating detailed topography or composition images.
TEM: Transmits electrons through ultra-thin samples, offering atomic-level structure insights.
Context: SEM suits fracture surface analysis, while TEM examines dislocations, grain boundaries, or nanostructures. Preparation can be intricate (e.g., FIB milling).
5.3 Mechanical Testing (Tensile, Hardness)
Definition:
Tensile test: Stretch a specimen until failure, measuring yield stress, UTS, elongation.
Hardness test: Indent a surface (Brinell, Vickers, Rockwell) to gauge resistance to deformation.
Context: Mechanical tests confirm a material meets strength or ductility specs, essential for final part design acceptance.
5.4 DSC / TGA (Thermal Analysis)
Definition:
DSC (Differential Scanning Calorimetry): Measures heat flow changes during temperature ramps (melting, crystallisation).
TGA (Thermogravimetric Analysis): Tracks weight changes upon heating (e.g. decomposition, oxidation).
Context: Thermal analysis helps identify polymer glass transition temperatures, measure oxidation stability, or confirm doping levels in advanced materials.
6. Alloys, Polymers & Composites
6.1 Alloy
Definition: A mixture of metals (and sometimes non-metals) forming a single solid solution or multiple phases, typically optimising strength, corrosion resistance, or cost.
Context: E.g. steel (iron + carbon + alloying elements), bronze (copper + tin). Alloy design is a key domain for metallurgists.
6.2 Composite
Definition: A material combining at least two distinct substances—matrix (polymer, metal) and reinforcement (fibres, particles)—gaining superior properties.
Context: Carbon-fibre reinforced polymers exemplify high strength-to-weight ratios, widely used in aerospace or motorsport.
6.3 Thermoplastic vs. Thermoset
Definition:
Thermoplastic: Softens upon heating, can be repeatedly melted and reshaped (e.g. ABS, nylon).
Thermoset: Irreversibly cured, cannot be remelted (e.g. epoxy, phenolic resins).
Context: Thermoplastics suit recycling or injection moulding; thermosets excel in high-temperature or structural scenarios, though less recyclable.
6.4 Biomaterials
Definition: Materials (natural or synthetic) used within medical implants, prosthetics, or tissue engineering, interacting safely with living tissue.
Context: Biomaterials might be titanium alloys for joint replacements, biodegradable polymers for sutures, or scaffolds for regenerative medicine.
7. Quality, Standards & Sustainability
7.1 ISO 9001 & AS9100
Definition:
ISO 9001: A quality management system standard for general manufacturing.
AS9100: A similar QMS standard specific to aerospace, demanding higher rigour.
Context: Many materials suppliers pursue ISO/AS compliance to meet industry expectations—ensuring consistent production and traceability.
7.2 Six Sigma
Definition: A methodology aiming to eliminate defects or variability in processes, measured in sigma levels of process capability.
Context: Six Sigma projects reduce scrap or rework, beneficial in materials manufacturing. Tools like DMAIC help refine processes systematically.
7.3 Life-Cycle Assessment (LCA)
Definition: Evaluating environmental impacts of a product or material across its lifespan—from raw extraction through disposal or recycling.
Context: LCA suits sustainability goals. Minimising carbon footprint or resource depletion often influences material selection in design phases.
7.4 Circular Economy
Definition: A regenerative approach keeping materials in use for as long as possible—via recycling, remanufacturing, or upcycling—reducing waste and resource consumption.
Context: Circular economy principles guide design for disassembly, easy reprocessing, or modular repairs—particularly relevant in packaging, consumer electronics, or automotive parts.
8. Industry Applications & Emerging Trends
8.1 Aerospace & Defence
Definition: Materials with high strength-to-weight ratios, thermal stability, or corrosion resistance—like titanium alloys, carbon-fibre composites—underpin aircraft, satellites, or military gear.
Context: Strict certifications (AS9100), traceability, and reliability testing define aerospace/defence demands for advanced metals, composites, or ceramic matrix materials.
8.2 Automotive & Electric Vehicles
Definition: Lightweight metals (aluminium, magnesium), composites, or battery chemistries driving improved fuel economy or range. Innovations also address crash safety, durability, or cost.
Context: As EV production grows, materials enabling higher energy density or safer battery packs are in focus—like silicon anodes or solid electrolytes.
8.3 Electronics & Semiconductor Packaging
Definition: Materials for PCB substrates, solder alloys, thermal interface solutions, or advanced encapsulants. They must handle heat dissipation and fine-scale geometry.
Context: Semiconductor packaging merges mechanical and electrical requirements—exploiting low-k dielectrics, copper lead frames, or underfill resins in high-density chips.
8.4 Renewable Energy & Storage
Definition: Materials used in solar panels (silicon wafers, perovskites), wind turbine blades (glass/carbon composites), or battery cells (Li-ion electrodes).
Context: Renewables demand cost-effective, durable materials (e.g. corrosion-resistant metals for offshore wind). Energy storage R&D focuses on novel electrode chemistry or solid-state electrolytes.
9. Conclusion & Next Steps
From the simplest polymers in packaging to high-temperature alloys in jet engines, materials science underpins the entire supply chain of modern manufacturing and product innovation. By exploring foundational concepts—atomic structures, processing techniques, testing methods, or industry standards—you equip yourself to design, produce, or select optimal materials for specific uses. Additionally, staying attuned to sustainability and emerging technologies fosters better environmental stewardship and new commercial pathways.
Key Takeaways:
Core Knowledge: Understand microstructures, mechanical properties, and processing fundamentals for metals, ceramics, polymers, and composites.
Testing & QA: Characterisation methods (SEM, XRD, mechanical tests) drive robust data guiding design or compliance.
Industry Relevance: Different sectors (aerospace, automotive, electronics) each demand unique property sets—strength, conductivity, heat resistance, or lightweight design.
Sustainability & Circularity: Materials usage stands central to eco-friendly solutions. Innovations in recycling or biocompatibility shape the future.
Next Steps:
Deepen your specialism: Whether in composites design, metallurgical processes, or polymer chemistry, advanced training or academic collaboration can refine expertise.
Contribute to industry or open research—journals, conferences (e.g. MRS, TMS) provide networking, knowledge-sharing, and feedback.
Stay Updated on new materials (2D materials, high-entropy alloys, advanced ceramics) or emerging process methods (3D printing, automated fibre placement).
Explore Careers: Check www.materialssciencejobs.co.uk for roles matching your focus—R&D, testing, QA, manufacturing, or commercial strategy.
Connect with Materials Science Jobs UK on LinkedIn to find job leads, share breakthroughs, and join a community of experts driving the next wave of materials innovation.
By mastering these terms and continuously updating your skill set, you’ll not only speak the language of materials science but also contribute to groundbreaking technologies that shape a more advanced, sustainable world.