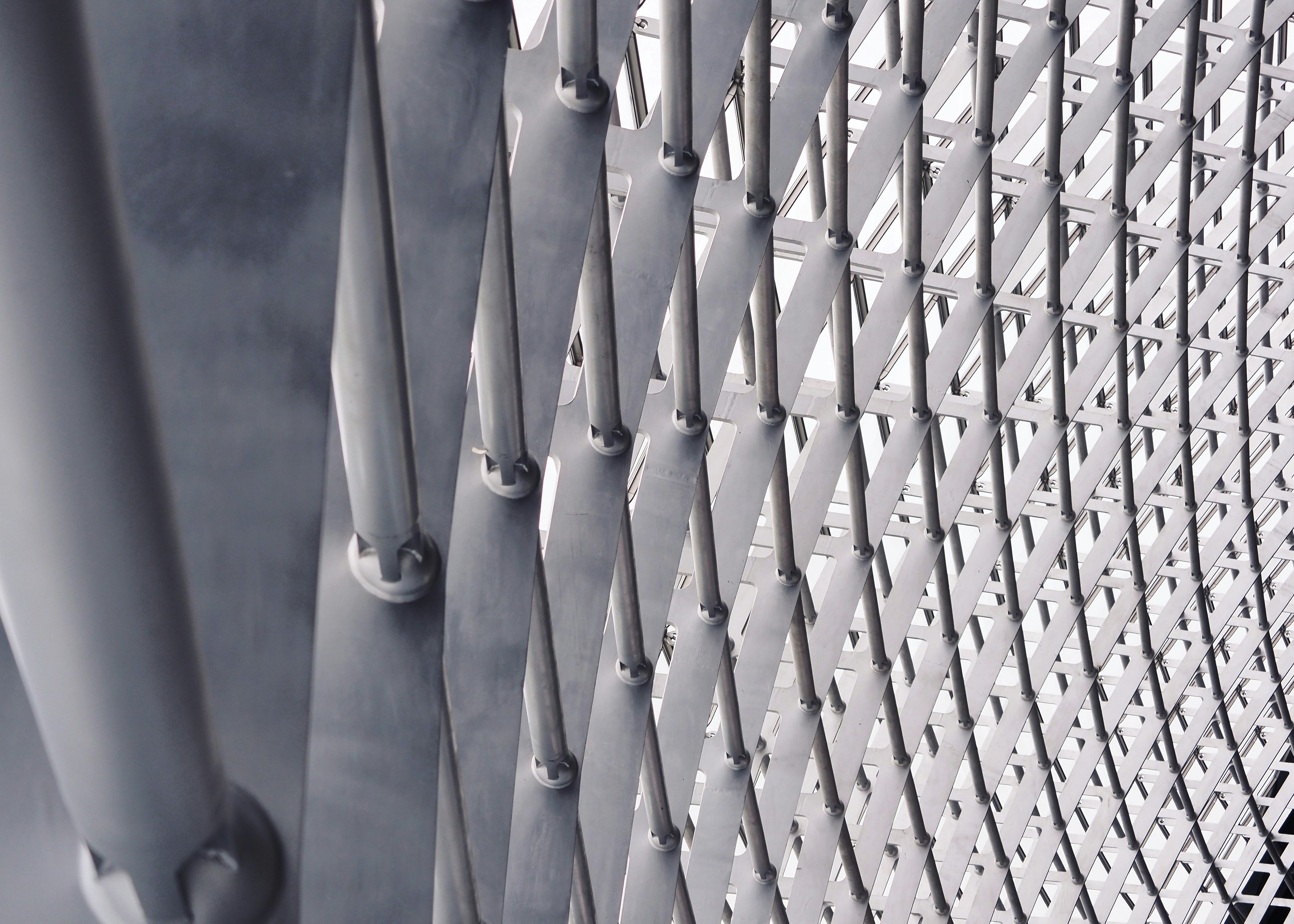
Return-to-Work Pathways: Relaunch Your Materials Science Career with Returnships, Flexible & Hybrid Roles
Re-entering the workforce after a career break can feel daunting—especially in a specialised field like materials science. Whether you paused for parenting, caring responsibilities or another life chapter, the UK’s materials science sector now offers a range of return-to-work pathways. From structured returnships to flexible and hybrid roles, these programmes recognise the transferable skills and resilience you’ve gained, pairing you with mentorship, targeted upskilling and supportive networks to ease your transition back. In this guide, you’ll discover how to: Understand the current demand for materials science talent in the UK Leverage your organisational, communication and problem-solving skills in materials contexts Overcome common re-entry challenges with practical solutions Refresh technical knowledge through targeted learning Access returnship and re-entry programmes tailored to materials science Find roles that accommodate family commitments—whether flexible, hybrid or full-time Balance your career relaunch with caring responsibilities Master applications, interviews and networking specific to materials science Learn from inspiring returner success stories Get answers to common questions in our FAQ section Whether you aim to return as a research scientist, process engineer, quality specialist or R&D manager, this article will map out the steps and resources you need to reignite your materials science career.